Shoes are a life-necessity that many designers and trends have turned into a fashion statement. While many international names dominate the global market, Egypt is full of fashion savvies that would never be satisfied with whatever number of pairs they have.
With technology molding and driving the fashion industry, footwear is becoming an area where innovation is key. Even though many women would risk personal comfort for extravagance, new methods and trends promise statement without pain.
Despite the fact that Egypt has always been known for exceptional leather and well-established factories, footwear is not a specialty that many young designers decide to pursue.
Jayda Hany is an exception to the ordinary. The promising designer seeks to push boundaries and design limitations in order to reinterpret shoe wear across the globe. The avant-garde designer depends on cutting-edge technology to create show-stopping shoes.
Her first collection did not only establish a base of impressed fans, it has also positioned her very young brand as a unique and technology-forward label that is home grown. Her handful of designs have immaculately created to suit top-notch stage performances of international artists. Meanwhile, comfort is a key factor that Hany considers at the core of her aesthetic.
Daily News Egypt sat with local designer to speak shoe wear, inspiration, and wearable technology.
In your opinion, why does Egypt have few outstanding bag designers, but not as many in the area of footwear?
Shoes are very difficult, because you have to design the sole and heels, especially if you want to do your own unique design. It is very possible to source ready-made soles and heels from local suppliers; they import them from China. Nonetheless, they will not be my design, they will not have my logo on them, and they will end up looking like other well-known commercial designs.
Shoes require patience. Each design needs several samples before it is ready. Every sample needs several trials to test convenience and comfort for the wearer. The trickiest aspect is often the foundation: sole and last.
How does your creative and manufacturing process unfold?
I start designing my own pieces from scratch, and then I 3D modeled them, before scouting for manufacturers that would meet my standards of quality in the shortest timeframe and with the most reasonable price.
Your shoes are notorious for mixing height and absolute comfort. Tell us more about the science invested in this mixture.
Making high heels is very different from flats. Flats are all about the sole; meanwhile, high heels are based on the last. Accordingly, it is an equation of how high you aim to design the final shoes, the height of the shoe-last, and the toe shape.
The highest and least-comfortable shoe last is 13 centimetres, and they are not known for being practical or convenient. Therefore, platforms are essential to balance height.
I have tried several methods for high heels, and I have decided to follow a certain technique. For example, I try not to exceed 11 or 12 centimetres for the shoe last; meanwhile, I play with the platform. At the end of the day, I want my shoes to look magnificent and eccentric; but, I still want people to be able to wear them.
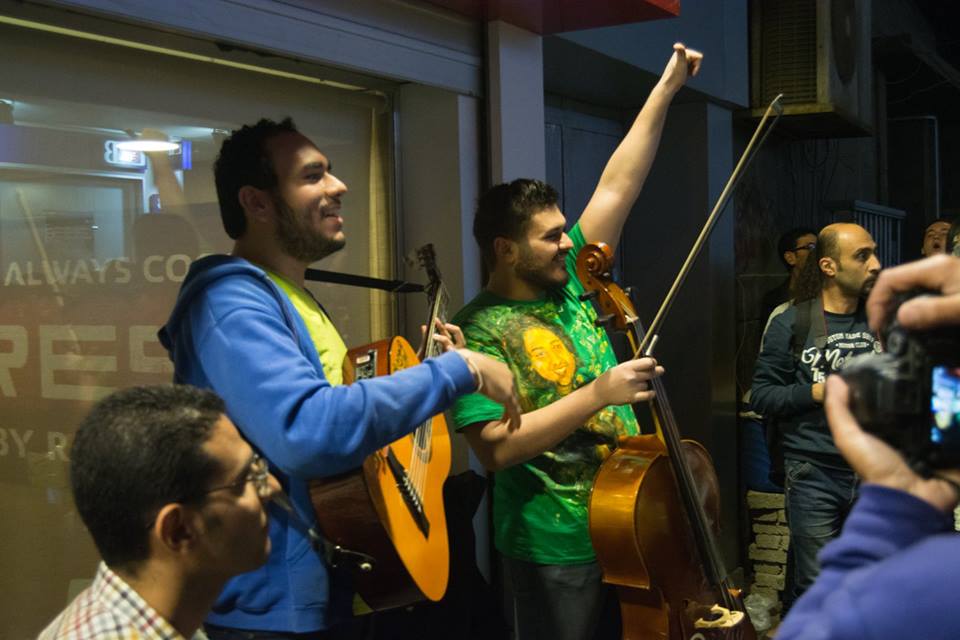
(Photo from Facebook)
What is the main element that separates your brand from any other similar avant-garde labels?
What separates me from other avant-garde designers is that my designs are eccentric and unique; yet, they are practical.
For example, other brands around the world that depend on 3D printing are often not quite wearable. Meanwhile, I utilise technology to create practical products. I integrate several materials and technology to create the end result.
What are the main technology methods that you depend on?
My first collection depended on two main techniques: 3D printing as well as CNC milling. The difference is basically that 3D gives you the opportunity to build out of nothing. On the other hand, CNC milling depends on negative space; products are engraved into a block of material.
CNC is ideal for surfaces, while 3D printing is more appropriate for angles and shapes.
How long did it take you to create your first collection?
For me, designing goes under research. For my first collection, it took me nine months of research; it was my master collection, and I wanted to invent a new way to “build” shoes.
I did not want to “create” a new collection; instead, I wanted to approach shoes as if they were buildings and construct something new. The second I was satisfied with my research conclusions, I started sketching then manufacturing.
Why are you keen on producing in Egypt?
We have everything in Egypt. For example, the leather that you see at the greatest leather exhibitions around the world is actually imported from Egypt. We have three key tanneries that export leather to the rest of the world. High-end brands—such as Chanel, Valentino, Fendi—depend on Egyptian leather.
Local leather is by far the best in the world. We have the most convenient climate worldwide, as the temperature is almost always moderate, which is key to the leather tanning process. On the other hand, the way cows are domesticated in Egypt positively affects the leather’s quality.
That said, fashion technology is highly attainable in Egypt. People are under the impression that we do not have 3D printing in Egypt. On contrary, we have a lot of printing houses. The only problem that we truly face in Egypt is the lack of certain materials; however, we have many low-key suppliers that provide suitable alternatives.
How did you manage to shift from your architectural background to fashion designing?
It was my backup plan. I have always wanted to design womenswear since I was 10. My parents were very supportive; yet, they were concerned about me pursuing a career in fashion during a time when Egyptians did not have an established industry.
As an alternative, my parents suggested that I pursue architecture, since it was a safe option at the time. Surprisingly, I did not oppose that suggestion. After five years of studying architecture, I took a year off before applying to the London College of Fashion.
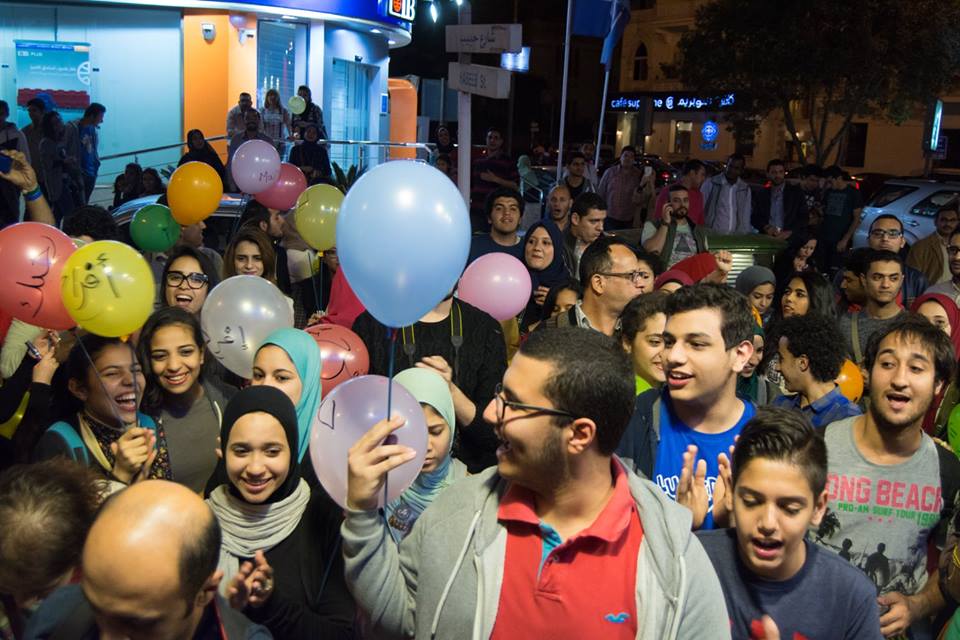
(Photo from Facebook)
What made you specialise in footwear in particular?
My first option was womenswear. However, I did not mind putting footwear as my second option in London College of Fashion’s application.
During my interview with a board member, I had a huge portfolio of womenswear that included complementary pairs of shoes for every outfit. Furthermore, it also included two shoe designs at the very end.
The board member went through the portfolio and kept looking at the shoes. She then flipped the portfolio on the other side, got to the last two pages, and said that these pages are what will get me into the London College of Fashion.
How did your five years in architecture influence your design aesthetic?
When you study architecture for five years, you start having a better understanding of structure and foundation; you always tend to start from the bottom. Subconsciously, this affects my fashion sketches. Hence, shoes have always been the strongest point in all my sketches.
On the other hand, I aim to honour and respect the wearer’s intelligence. As a customer, I like to examine and see what each piece is made of. I like to analyse the design and the materials used. I wanted to convey this sort of understanding to the people who will at least check my shoes; I want them to feel intelligent.
Who is your ideal target audience?
As a brand, I have the bespoke line that targets performers and celebrities because it represents quite an eccentric statement. On the other hand, I have got the commercial, ready-to-wear line, which includes everything from high heels to trainers, which target a much wider selection of people.
What are your near-future plans?
I am launching my first autumn/winter collection very soon. I always work and design a year in advance; however, manufacturing takes a much longer period of time. Between designing and producing, I am always running around, researching and experimenting with new suppliers and concepts.